Valve actuators are common in industrial and residential sectors. Without a valve actuator, the valve won't direct or regulate the fluids. All residential and industrial valves operate on a few types of actuators: spring return and double-acting, fail-safe and non-fail-safe. But which one should you buy?
Keep reading to learn more about the advantages, disadvantages, and other specificities of these valve actuators.
What Is an Actuator Valve?
So, let's start with the basics and explain the function of valve actuators.
Every valve needs a power source to work. The valve actuator is a mechanism that provides the energy to regulate the flow of fluids.
Now, how does a valve actuator work? All pneumatic, hydraulic, and electric actuators convert the energy source into the rotary force to move the valve plug into the desired position. In simpler terms, this mechanism opens and closes the valve to allow the fluids to flow.
The operating principle depends on the energy source. Based on this principle, the actuator can be either manual (a man-powered mechanism) or automated.
The most popular automated actuators include:
- Pneumatic valve actuators: Pneumatic actuators use compressed air to power up the valve.
- Electric actuators: Electric actuators use electric current to provide torque.
- Hydraulic actuators: Hydraulic valve actuators convert fluid pressure to operate valves.
Now, let's discuss the different types of valve actuators: fail-safe and non fail-safe, spring-based and double-acting.
Shop for top brands like Belimo, Siemens, and Honeywell now at Blackhawk Supply store!
DAMPER ACTUATORS FOR SALEWhat Is a Fail-Safe Actuator?
Manual valve actuators convert energy to create physical motion inside the valve. With an actuator, your valve will be able to open and close, allowing the fluids to flow. Therefore, valve actuators are an essential part of the HVAC (heating, ventilation, and air conditioning) and plumbing systems.
A fail-safe valve actuator is a mechanism that returns the valve to a safe position if it loses the power supply. This type of actuator is common in commercial and industrial environments because it's much more reliable.
Here's an example. If you lose electricity on a cold day, the air damper won't get stuck in the open position with a fail-safe actuator, meaning the coil won't freeze inside and break. This makes valve actuators with fail-safe mechanisms an excellent choice for applications that experience shutdowns often.
Features
-
Fail-safe valve actuators have great durability and support for strong thrust and torque.
-
Reduces the maintenance costs and increases the service life of valves, plumbing systems, and other HVAC appliances.
-
Programmable fail-safe positioning (can either open or close after the power is cut).
-
Optimizes energy consumption.
-
A great option for BAS (Building Automation System) and HVAC applications that require protection against electric overloads, as well as for environments where the power can shut down often.
-
Excellent choice for applications where the load is supplied to one side of the piston.
-
Variety of rotary, linear, and quick running products for challenging applications.
Types
A fail-safe valve actuator should be able to return the valve to opened or closed position in case of power outages. What kind of mechanism can ensure that the valve will move to the original desired position?
The two main types of fail-safe actuators are:
-
Spring-return actuators. The valve is moved to the operating position while the air compresses the spring mechanism. The energy in the spring is released after the power cuts off, either opening or closing the valve.
-
Battery backup actuators (capacitors). Smaller, customizable, and more durable actuator mechanism. This actuator relies on an alternative power source to move the valve after losing connection to the power source.
The first spring-return actuators used air pressure to push the diaphragm to keep the spring compressed. Electric actuators were introduced later on and initially didn't have a fail-safe. In time, the mechanism was added to make them open or close the valve after losing the power.
Spring-return devices support up to 27,000 automation, meaning they're not the best option for frequent usage (like throttling and control applications). The battery backup actuators can take over a million automation. Plus, they cost less than standard pneumatic actuators, making them a perfect option for most systems.
What Is a Non Fail-Safe Actuator?
Now, let's talk about valve actuators without a fail-safe mechanism.
A non fail-safe actuator will keep the valve tightly secured if the valve loses connection to the power source. These actuators have excellent thrust strength that ensures the valve will retain its last position.
This type of mechanism is typically used in high thrust applications. For example, non-fail-safe valve actuators work excellent for gate movement, gas and oil applications.
Features
-
Non-fail-safe actuators work great for higher torque loads and thrust applications (such as oil and gas applications).
-
An excellent option for applications with the load on both working directions of the piston.
-
Brushless DC motors ensure long-lasting service life and reliability.
-
Minimal torque due without the speed, temperature, or performance compromises, thanks to an application-specific integrated circuit.
-
Variety of models with different control types.
-
Typically comes with an extended warranty (about five years or more).
-
Easy to mount and set up.
What Type of Actuator Should I Get: Fail-Safe or Non-Fail-Safe?
Now, what are the pros and cons of actuators of fail-safe and non-fail safe mechanisms?
The fail-safe actuators return the valve to a pre-set position in case of a power outage. This mechanism is by far the most popular in commercial environments. They are highly reliable, straightforward, and offer the most protection for your applications.
Fail-safe actuators are best used for applications with torque loads on one side of the piston or those that require protection against overheating and freezing.
Non-fail-safe applications keep the valve in place after it loses the energy source. They are mostly used for applications with torque load on both sides of the piston, such as gate movement, oil and gas regulation equipment.
Spring Actuators vs. Double Acting Actuators
All automated valve actuators use a spring return or a double-acting mechanism. Let's see what makes them different to help you understand which one will work best for you.
Spring Return Actuator

The spring return valve actuator (also known as a single-acting actuator) delivers the compressed air or liquid to one side of the piston. The pressure creates the force that moves the spring mechanism on the other side of the valve. As a result, the spring opens and closes the valve, regulating the flow.
The single-acting actuator is the most common mechanism for flow regulation. What makes it so popular?
The advantages of these actuators include:
-
Straightforward design.
-
Great durability and reliability.
-
Excellent fail-safe technology.
The spring return mechanism has strong thrust and torque. It's especially good for applications with a high torque load on one side of the piston.
A single-acting (spring return) actuator will either close or open the valve if it loses the energy supply. Therefore, it will work best for applications that could shut down often.
Double Acting Actuator
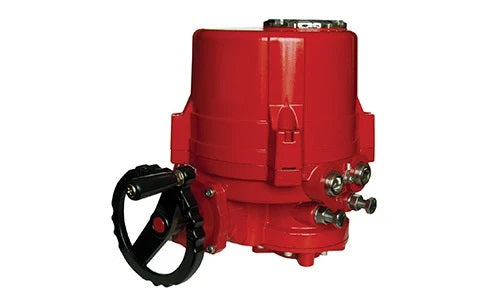
mechanism delivers the energy source (liquid of compressed air) to both sides of the piston. When one side gets more pressure, it creates a movement that opens or closes the valve.
This type of valve works best for high thrust applications, such as gate movement or natural gas applications.
The double-acting valve actuators have several benefits, such as:
-
Higher torque loads.
-
Exceptional thrust strength.
-
Keeps the valve secure in the last position in case it loses signal.
The pressure on both sides of the valve keeps it tightly secured in case of power outages. Therefore, double-acting actuators are the best option if you need the valve to retain the last position after losing power.
How to Choose the Right Actuator: Double Acting or Spring Return
Now you should know the defining characteristic between double acting and spring return actuators. But how do you pick the right one?
Let's help you choose a suitable actuator for your applications.
Torque & Thrust
Thrust strength and torque are pretty much equal in spring return and double-acting actuators. A single-acting actuator works excellent for applications where the load is supplied to one side of the piston.
In some situations, the double-acting mechanism will work better. This type of actuator is perfect for natural gas and oil applications with extreme torque load in both working flow directions.
Control
The double-acting mechanism provides the best stability overall. It's especially useful when sudden changes in process conditions are frequent.
Safety
Most system applications require the valve to be open (or closed) when the energy source is gone. The spring return actuator is the most straightforward and reliable option in these cases.
Last Position
As we mentioned, a single return actuator works best for applications where a valve should open or close after it loses power.
However, sometimes you'd want to retain the last failed position. In that case, you should go with a double-acting actuator.
Comparison Table: Spring Return vs. Double Acting Actuator
Are you short on time? Don't worry — here's our quick summary of both actuator types.
Type of Application | Spring Return Actuator | Double Acting Actuator |
Torque & Thrust | For applications with torque load on one side of the piston | For applications with extreme torque load on both sides of the piston |
Control | Up to 8-inch valves | High thrust applications with more than 10-inch valves |
Safety | Extremely reliable and straightforward | Too complex for most safety applications |
Last position | Valve returns to the open/closed position when the power supply is gone | Valve retains the last position when the power supply is gone |
Conclusion
There's no universal solution for your valves. Single-acting and double-acting actuators have their advantages and use cases. But we hope we could shed some light on these mechanisms to help you pick the right one!
Do you want help selecting valve actuators for your systems? Blackhawk Supply offers a wide range of valve and damper actuators, and other supplies for industrial and residential buildings. Find the right equipment for your needs today!